Satellite batteries – for CubeSats, nanosats, and other form factors
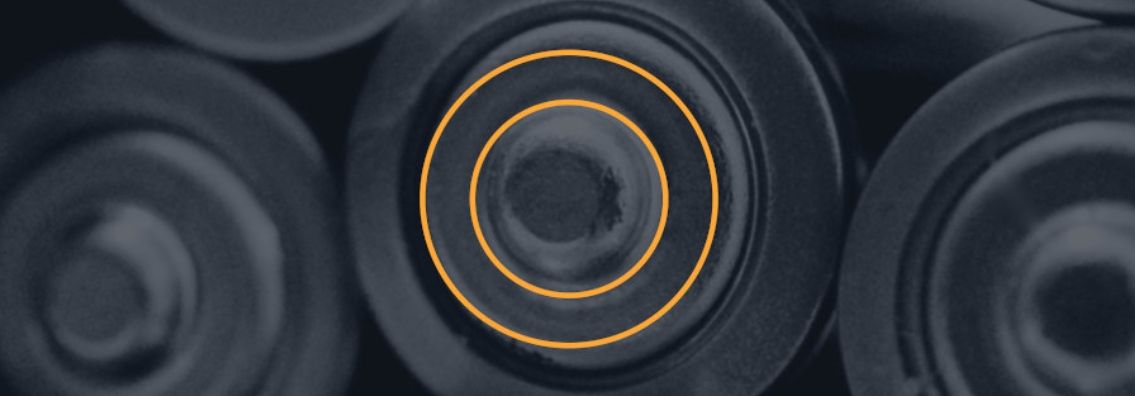
Satellite batteries – for CubeSats, nanosats, and other form factors
Energy generation and management is an important aspect of electrical power sub-systems. Secondary batteries store the generated electrical energy from solar energy, and power the satellite when the sun is eclipsed, or too far away during the mission to give enough direct power.
Secondary (rechargeable) batteries are the focus of this article, with well-known examples being Lithium-ion or Lithium-based batteries adapted in space applications.
This article gives a brief overview of satellite battery technology and shares details of commercial-off-the-shelf (COTS) battery products from around the world. If you are familiar with the technology and would like to skip straight to the product listings, please click here.
What are space-graded batteries?
The primary source of energy in a microsatellite (satellites with deployed mass up to 100 kg) power system is solar/photovoltaic panels, which convert solar energy to electrical energy, while batteries are the secondary source.
Batteries convert electrical energy to chemical energy during charging, and perform the opposite process during discharge. A typical battery contains a negative and positive electrode immersed in an electrolyte, separated by an insulator.
Primary and secondary batteries are two types of power storage systems that are used in satellite power systems, classified based on their electrochemistry.
For short missions primary batteries are used, as they are not rechargeable. For repeated cycles of usage, as in the case of eclipsed seasons, secondary (rechargeable) batteries are preferred.
Typically, nickel-cadmium (NiCd), nickel-hydrogen (NiH2), lithium polymer (LiPo), and lithium-ion (Li-ion) cells are used as secondary batteries in space applications.
For any object to be space-graded, it has to withstand severe vibration during the launch, vacuum pressure once it reaches the designated orbit, and extreme temperature, and solar radiations at different stages.
Every satellite sub-system has to be designed and tested for such extreme environmental conditions. Despite such challenges, it is also expected in the modern industry that every component should have increasingly longer lifetimes, higher efficiencies, and, more importantly, is available at a comparatively lower cost.
The challenges of the space environment
To be able to reliably use satellite batteries on-board space systems, environmental conditions become even more important to be considered in design, as it can be possible for battery systems to leak, or even explode.
Some of the important parameters to consider for selecting the right set of batteries include; depth of discharge (DOD), shelf-life, ability to recharge, power capacity (in Ah), weight, operating temperature range, resistance to shock and vibration, power management schemes, charge cycles, specific energy, cost, and ruggedness. More information on such criteria is given below.
Another of the common issues with satellite battery technology is overcharging. It should also be considered during the design and testing phase to avoid the risk of overheating once the maximum voltage is reached. Overheating may lead to explosion or fire, which would likely be catastrophic to a mission.
Finally, other undesirable conditions for a battery would include short circuiting, an operating temperature higher or lower than the designed range, exceeding the preset limits of the DOD, a build up of pressure inside the cell due to the chemical reactions, and excessive current developing.
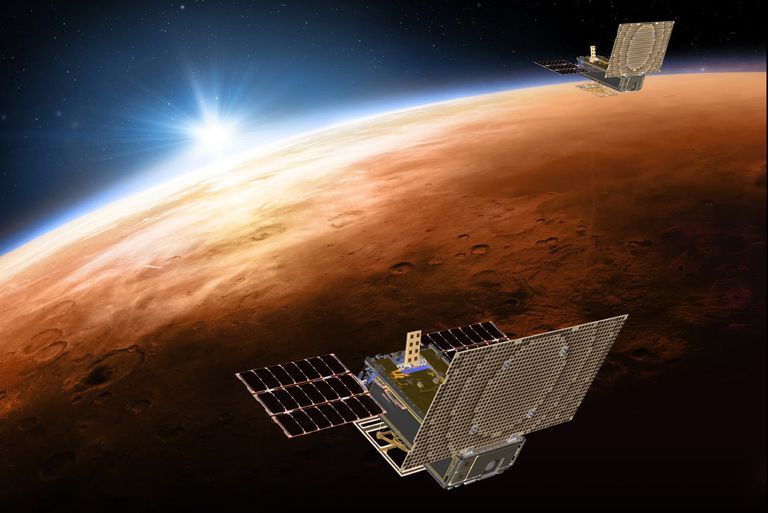
As you can see, developing a battery to work in space is no easy task, particularly as they play such an important role. And the core of any battery system, which needs to meet these challenges, is the fundamental chemistry of the energy-storing cells.
The types of batteries used in space
The reliability of a battery depends mainly on the choice of the electrochemical system it is based on. Among the many different types, the most widely used batteries are Nickel–Cadmium (NiCad), Nickel–Hydrogen (NiH2), and Lithium-ion (Li-ion) batteries. These are described in more detail below:
Ni-Cd
Although NiH2 and Lithium-based batteries are sometimes thought to be replacing Ni-Cd batteries in newer systems, this format has served as an effective storage system for decades, with an adequate lifetime and fair capacity, satisfying the requirements for space missions in the past. The cathode (positive electrode) of these batteries is nickel and the anode (negative electrode) is cadmium, and potassium hydroxide is used as the electrolyte. These batteries have been in use on LEO and GEO satellites.
Ni-Cd battery technology is mature. The systems are lightweight and inexpensive, but usually not as energy-dense compared to other forms. Their ability to deliver the full capacity with a high discharge rate is one of the significant advantages of the batteries.
Notable flaws in such batteries are that the high charging rate can cause overcharging and overheating causing damages to the battery. Prolonged usage of these batteries may also cause holes in the insulator material where crystalline “shorts” are grown. When this occurs, the cell can charge only if these crystallines are opened by high pulse current.
Nickel–Hydrogen (NiH2)
Nickel-Hydrogen secondary batteries are designed exclusively for space applications. They are an example of a hybrid between fuel cells and battery technology. The electrodes of the cells are made of positive nickel hydroxide and negative platinum catalyst. The cell case serves as the pressure vessel for holding the negative hydrogen gas.
The main advantage of Nickel-Hydrogen batteries is that they do not pose a safety issue while overcharging or overdischarging. They also provide a higher specific energy compared to Ni-Cd batteries. The main shortcomings are that they have a high self discharge rate, low volumetric energy density, and require high pressure storage to hold the hydrogen gas generated during charging.
A classic example is the Nickel-Hydrogen batteries powering the Hubble Telescope in LEO, which were in operation from its launch in 1990 to 2009, and were thenthen replaced by improved versions of the same type of system.
Li-ion
Lithiumi-ion batteries are known for their dense energy, longer lifetime, and rechargeable capacity. Since Li-ion batteries became commercially viable products in 1991, they have been adapted in multiple industrial applications, including the space industry.
The highlights of Li-ion battery characteristics include a wide range of operating temperatures, and a prominent working cycle. The systems are also capable of delivering short and high energy peaks without affecting the cell. The Li-ion cell characteristics differ based on the cathode material, while the anode is typically a carbon-based material.
Lithium manganese oxide (LMO) and Lithium manganese nickel (NMC) cells are low cost and have reasonable safety ratings among Li-ion cells. LMO cells have low specific energy and high discharge rate capability, while NMC cells have high specific energy, low resistance and low discharge rate capability.
Lithium nickel cobalt aluminum oxide (NCA) cells have the highest cycle life and specific energy among the Li-ion cells with a low discharge rate capability and decent safety. Lithium nickel cobalt oxide (NCO) cells are rarely used. Lithium cobalt oxide (LCO) cells are expensive, characterized by low specific energy, poor safety and lower discharge rate capability. Lithium iron phosphate (LFP) cells are characterized by their low specific energy, and high discharge rate capability with, good safety ratings.
Li-ion cells develop internal resistance rapidly at low temperatures posing a limitation to the discharge. Capacitors are used with Li-ion batteries as a hybrid system to improve their performance at low temperatures. Li-ion batteries are considered to be in class 9 of dangerous goods by the United Nations (UN), and so specific regulations of safety should be followed when in use of this product.
Batteries requirements by orbit
The mission’s orbit is a critical parameter to be considered for choosing a COTS battery. The required battery cycles change with the season and duration of the eclipses experienced by the satellites in different orbits.
Depending on the mission orbit (GEO or MEO or LEO), the specific energy of the battery also varies. In this section, an outline of eclipse seasons are provided to highlight the significant differences in the requirements of the stored power in the batteries.
LEO – a satellite in Low Earth Orbit (LEO) experiences a range of 5,000 – 5,500 cycles of eclipses over a year with a duration of 30 – 40 minutes each. These eclipses happen approximately every 90 minutes, as the satellites in LEO are positioned comparatively lower and complete a revolution faster.
GEO – a satellite in Geosynchronous Orbit (GEO) is positioned on the equatorial plane, focussing on the same geographical location by rotating at the same orbit speed as earth. It experiences a range of 90 – 100 cycles of eclipses in total, with two 45-day sessions over a year. The maximum duration of battery usage during this season is 72 minutes per day.
MEO – satellites positioned in the Medium Earth Orbit (MEO) face 170 cycles of eclipses per year. Typically, the eclipse duration ranges from 0-80 minutes. There are two seasons of eclipse spanning for a period of 40 – 60 days, per year.
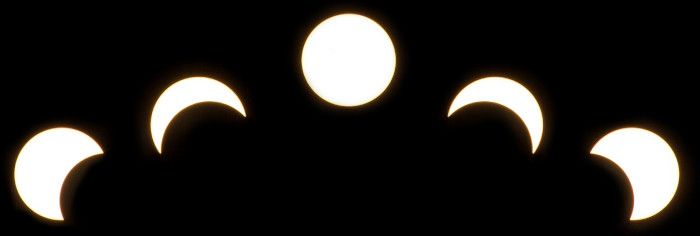
Orbit is very important to consider, but is just one of the criteria that need to be weighed up when selecting the right satellite battery for your mission.
Understanding your requirements
We recommend a simple four-step approach for the preliminary selection of any new piece of hardware or software for a satellite or other space system.
Note that this is just a basic guide based on what we’ve learned helping hundreds of buyers select products within our marketplace and get rapid responses from suppliers.
It is just meant to help engineers make an initial assessment and shouldn’t replace formalised systems engineering approaches such as the INCOSE Model-Based Systems Engineering (MBSE) CubeSat frameworks.
Specify your currently known mission parameters,
Record all currently known overall design specifications of the system,
Consider the range of technology that will be used in the satellite and in ancillary sub-systems, and
Take into account the key performance criteria of the kind of product you wish to procure.
These criteria are explained in more detail below.
Mission parameters
The first step is to fully understand the currently known mission parameters, including both the critical applications and desirable, but not necessarily essential, objectives.
Typically the more precise mission parameters will only be established later in the process – usually iterated upon in a number of loops by considering the “system of systems.”
But having an idea of what functions your selected technology is likely to need to perform, and on what schedule and duration, will make selecting the most suitable model much easier.
Also consider the launch stresses, testing processes and regulatory compliance that the product will need to go through in order to make it into orbit, as well as any obsolescence procedures once the mission is complete.
Overall design specifications
Next, keep to hand all currently known design information about the entire unit.
This can include the volume, weight, primary structural material and more basic things such as the location, storage and transport arrangements of the major components.
You will need to make sure that the new piece of technology you choose will be suitable for these parameters.
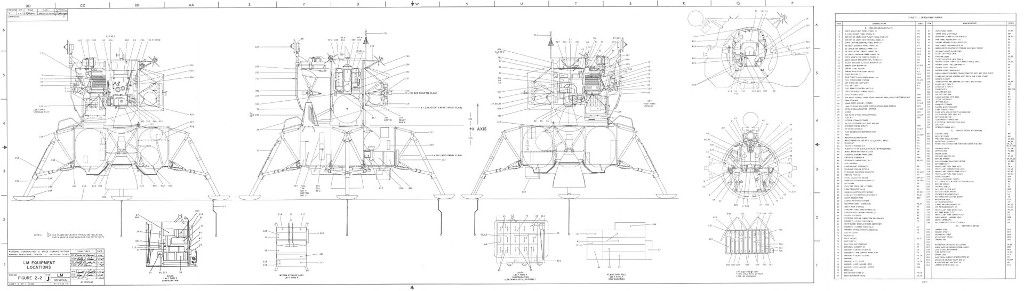
Full range of technology
Once you are clear on exactly what tasks the new product will need to perform and the design characteristics of the satellite or other unit that it will work within, the next consideration is the full range of technology that will sit alongside the product to make sure that everything is compatible.
You may not yet know the entire range of accompanying technology (and you might need to first choose the product model you are interested in in order to make decisions on other components), but make sure you have access to all available technical specifications of sub-systems and structural components that are most likely to be used, as per the current mission plans.
It is important to understand how different sub-systems and components will interface with each other to create a high-performing satellite.
Balancing the available mass, power and volume budgets is also important, which can only be done with a clear plan of which components will be used.
Also consider how the product will work with the planned or existing ground segment to ensure effective data transfer and communication stability.
Now that you have a clear idea of what sort of product is needed for your mission, system, and existing platform setup, the next step is to compare the commercially-available products that meet these criteria according to the most relevant performance metrics.
Key performance criteria for satellite batteries
The following criteria are some of the main technical attributes to consider when selecting a battery for a mission or service.
Battery capacity – capacity is defined as the charge stored by the battery and is determined by the mass of active material contained in the battery. Measured in Ampere-hour, Ah.
Battery voltage – the difference in electric potential between the positive and negative terminals of a battery. Measured in V.
Battery Power – the amount of energy stored in the battery. Measured in Watt-hour, Wh.
Battery cell configuration – the physical arrangement of cells, for example:
Series arrangement: to obtain the required voltage at the bus and is denoted as ‘s’. The higher the required voltage, higher is the number of cells required in series.
Parallel arrangement: to obtain the necessary capacity.
S–P topology: the battery cells are assembled in series and then connected in parallel.
P-S topology: the battery cells are assembled in parallel as a module to provide the required battery capacity and then connected in series to meet the required voltage range.
Type of battery – as outlined in the previous section, the chemical composition of the batteries define their type.
Physical mass – the weight of the battery pack. Measured in grams or kilograms.
Depth of discharge (DoD) – the percentage of the discharged capacity as compared to the nominal capacity.
Satellite batteries on the global market
In the section below you can find a variety of commercially-available satellite batteries on the global market. We have also published an overview of satellite Electrical Power Systems (EPS) on the global market.
These listings will be amended when new products are added to the global marketplace, or existing systems are upgraded, so please check back for more, or sign up for our mailing list for all the updates.